Agricultural engineers develop device to prevent sunflower harvest combine fires
Harvesting sunflowers requires nerves of steel. “It’s not if we will have a combine fire, but when,†say producers. A team of South Dakota State University agricultural engineers may have found an answer to this nerve-wracking problem.
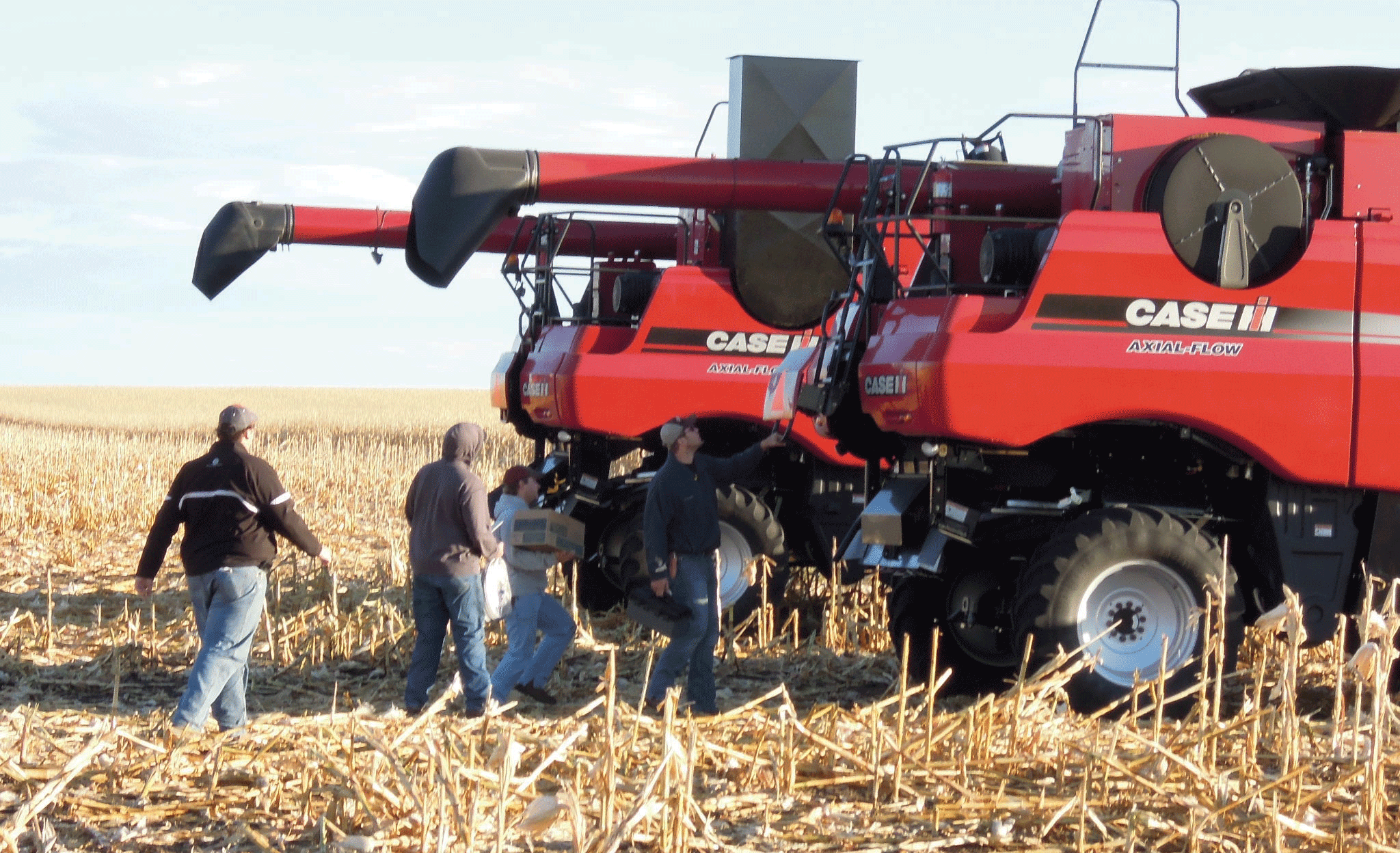
Students on the agricultural engineering team—Adam Wiest, Luke Bunkers, Evan Schnabel and Kyle Stewart—examine the Case IH combine to identify possible ignition sites. Next, they will outfit it with thermocouples to determine the hot spots.
The researchers designed and tested a device during two harvest seasons that has proven to drastically reduce and perhaps even eliminate these fires.
“Sunflower producers have known for a long time that they had a more severe risk of fire than producers of corn, soybeans or wheat,†said professor Dan Humburg, who leads the engineering team. His colleague, Kevin Dalsted, coordinates data-gathering and input from area producers and assists with technical and design work.
The South Dakota Oilseeds Council initiated the research in fall 2011 and the National Sunflower Association adopted and expanded the project in 2013. This year SDSU Technology Transfer Office Director Will Aylor is talking to companies interested in manufacturing the device for existing combines.
Protecting machines with vigilance
“Some producers won’t grow sunflowers because they don’t want to put their combines at risk,†Humburg noted, estimating the cost of replacing a combine at $300,000, without the heads and other needed accessories.
Farmers who do usually carry water on the combines to extinguish small smoldering areas, Humburg explained. Many producers also “keep a truck at the end of the field with a water tank to put out a catastrophic fire.â€
Identifying ignition source
To analyze the problem, master’s student Joseph Polin, now a doctoral student at Iowa State, and assistant professor Zhengrong Gu found that sunflower debris ignites at temperatures that are 68 to 86 degrees Fahrenheit lower than corn or soybean residue. In addition, the researchers discovered that a large part of the debris sticking to the combine was the white pith, which is then drawn into the fan that pulls air through the radiator to cool the engine.
“A portion of this dust ignites when it hits the turbocharger and exhaust system,†Humburg said. “Once a fire starts, it’s easy for a spark to be relocated.†Many machine components—fiberglass shields, wiring harnesses, flexible hoses and plastic fuel tanks—can burn.
A greater engine load also increases the exhaust system’s temperature and the likelihood of fires, Humburg noted. Sunflower producers reported monitoring fuel usage and rated engine load to identify the point at which they will experience combine fires immediately.
Designing preventive measures
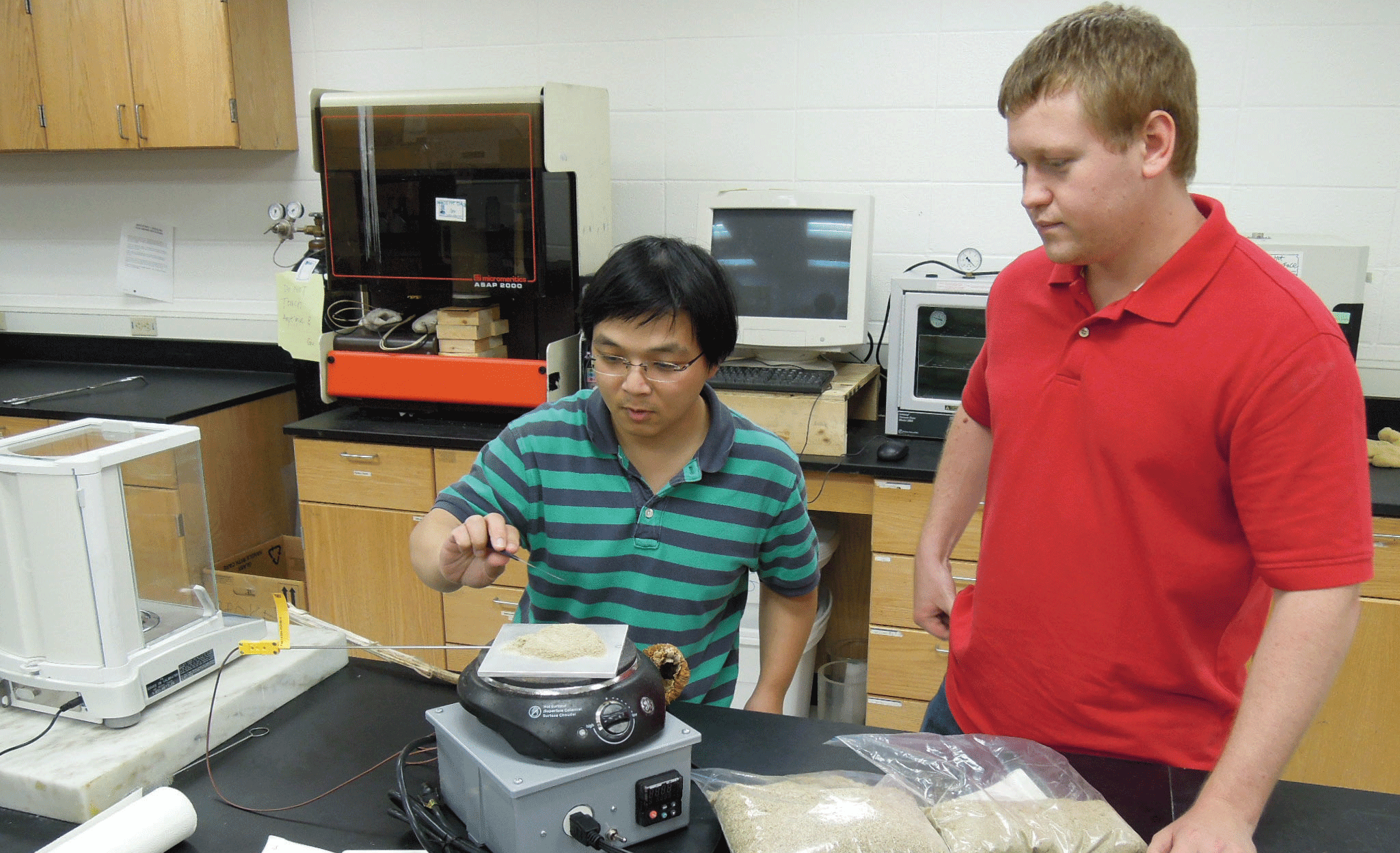
Assistant professor Zhengrong “Jimmy†Gu and graduate student Joseph Polin determine the ignition temperatures of sunflower head and stem particles. A chemical engineer from Massachusetts, Polin completed his master’s degree at SDSU and is working on a doctorate at Iowa State.
In fall 2012, the agricultural engineers tested a prototype system that uses a fan to pull outside air through a filter. The clean air is then pushed through a duct into an enclosure surrounding the turbocharger and exhaust manifold.
“This air that enters the hot environment contains no dust to ignite,†Humburg notes. Additionally, the outside of the patent-pending system easily stays within a safe temperature range.
Humburg credits producer Scott Foth for helping his team understand the problem. “I’ve been fighting these fires for years,†commented the Onida farmer. “I’ve experimented with many things that helped, but until now, nothing really solved the problem completely.†He used the prototype on his Case IH 8120 combine.
When a seal went out on the prototype system in 2012, Foth reported a fire every day until the device was repaired. He’s optimistic, but would like another harvest season under his belt before he’s totally convinced.
However, he added, “being able to go full speed and use all the capacity of the combine to get the crop in is a huge relief.â€
Following 2012 testing, Humburg and his team switched to a new air filter/precleaner system and used direct coupling of the hydraulic motor to the fan. However, sunflower fire risk during the sunflower harvest was low overall, so the SDSU team will continue evaluating the improved system this fall.
Producing promising results
The expertise and passion of the SDSU team produced results that Brad Bonhorst, former president of the S.D. Oilseeds Council, describes as having “great potential to solve the problem.â€
“This was one of the best uses of checkoff dollars that I’ve ever seen,†he said. “Those fellas took a relatively small amount of money and came up with some really impressive results.â€
In 2013, the National Sunflower Association took over funding the project, something that Bonhorst said “doesn’t happen very often.†The increase in funding allowed the researchers to expand the project to two more operations —another Onida farmer who has a John Deere 9770 combine and one in Hazen, N.D., who owns a Case IH 8230.
“All three models have different exhaust sizes and configurations,†Humburg explains, so the fan and filter system has to be redesigned for each combine. “That’s the limitation.â€
Humburg hopes to fabricate devices for one or two additional combine models, possibly a John Deere 9870 or 9670 or even a second 9770, this fall through extension of the National Sunflower Association funding.
“We will probably confine our experiments to John Deere and Case IH machines at this point, because they represent the bulk of the fleet used for sunflowers,†Humburg said. Farmers interested in participating can contact Humburg or Dalsted at 605-688-5141.
Getting device onto producers’ combines
The importance to producers is clear, but the challenge is figuring out the quickest way to get this technology into the hands of the producers, according to Aylor. That sense of urgency has led to negotiations with a fabrication company to manufacture the device for existing combines.
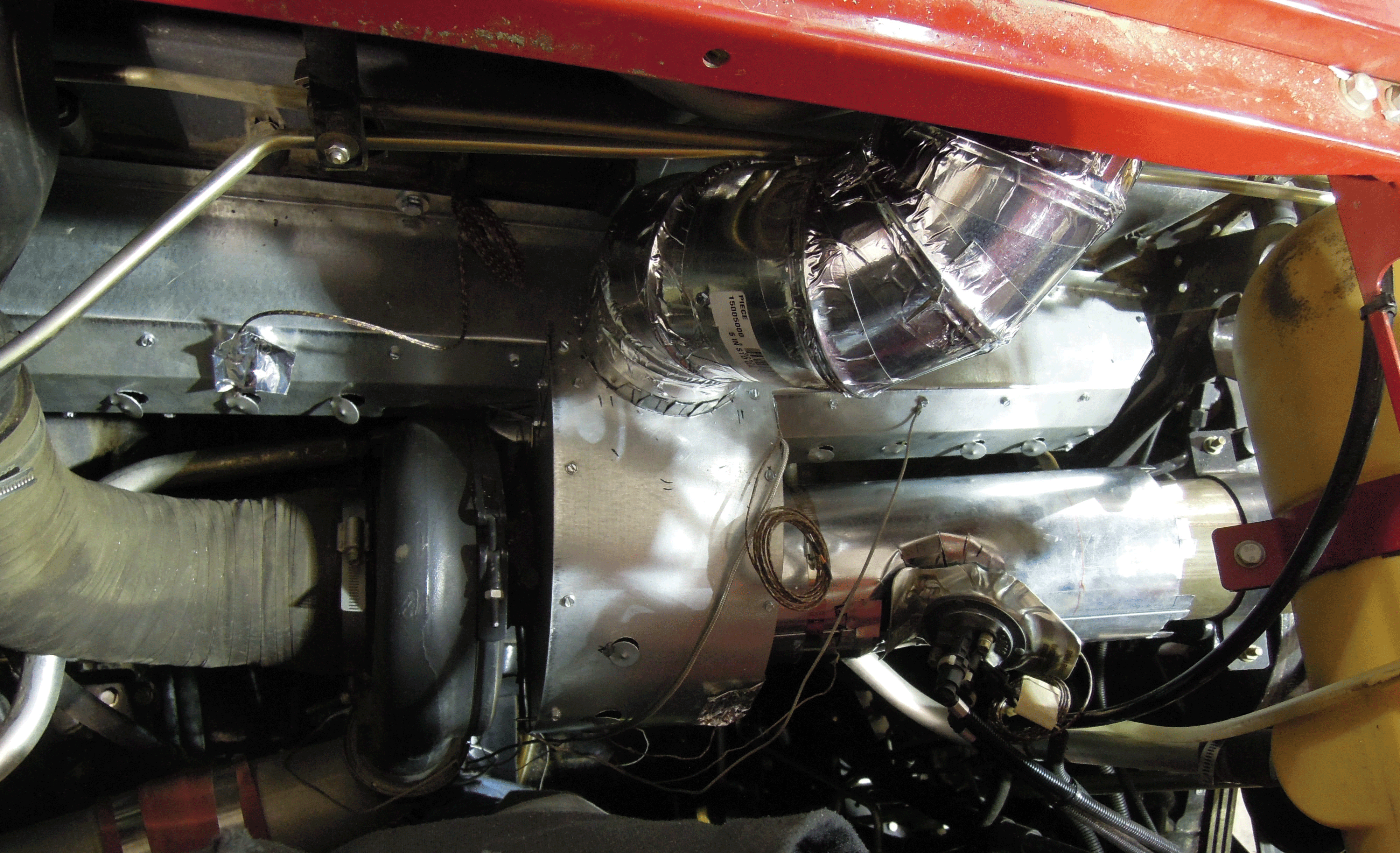
Filtered air is forced into the enclosure surrounding the exhaust components of this combine engine through the duct, center/right, and allowed to exit through the small vents in the center. This prevents sunflower debris from entering the compartment.
In addition, new diesel exhaust emission standards effective this year may make the devices even more crucial to producers, according to Humburg. To regenerate the diesel particulate filter that traps soot, manufacturers are running the component hot enough to burn the material away, creating another danger area when it comes to sunflower dust.
However, the researchers admit that sunflower growers do not constitute a large share of the combine market. In 2013, U.S. producers harvested 2.03 billion pounds, down 27 percent from 2012, according to the U.S. Department of Agriculture.
To build their case for the device, the researchers are looking at other crops, such as chickpeas, lentils and even soybeans that create an elevated fire hazard for producers. Humburg hopes that this type of equipment will become standard fare on combines.
“As a land-grant institution, we need to promote this as much as possible for the good it can do for producers,†noted Aylor. “It’s our mission.â€
Christie Delfanian